Aluminothermic welding* Kcup | by KLK
Technical articles KLK
Aluminothermic welding Kcup is the natural evolution of the exothermic process.
As a consequence of our strategy of constant product development, which helps us to offer more value to our customers, as well as to address more and more demanding markets, in the Welding line, the evolution of the welding called ‘k-cup’ has emerged.
Exothermic welding procedures are characterized by their ease and speed of execution. A few steps, carried out consecutively and in a very short time, are sufficient to complete the process and obtain the best weld. Hence the great value they offer. And also that everything that contributes to simplify the process even more will also contribute to increase this value.
Regarding the execution of our current welding process, the first steps have to do with the packaging format that has traditionally been used, that is, the plastic container with two compartments and two lids, each one of them to contain each of the two mixtures: aluminothermic powder and ignition powder.
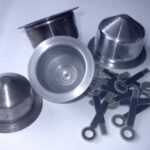
Imagen capsulas | Kcup weld
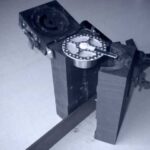
Imagen prototipo soldadura portátil | Kcup weld
Thus, it is necessary to place the disc at the bottom of the hopper, open the aluminothermic powder compartment and pour its contents, open the ignition powder compartment and pour its contents reserving a small quantity, place the ignition fuse inside the lid, pour the small quantity of ignition powder that had been reserved, and so on.
The k-cup is a further step in the simplification of the welding process, as it eliminates all the process steps involved in the traditional container format, requiring only a capsule to be placed in the mold hopper. In addition, it avoids having to handle any mixture, as it is neither uncapped nor poured, with the consequent reduction of risk for the user.
“K-cup allows its use in traditional molds and its connection by traditional ignition or by LSvip.”
Thus, the k-cup is, first and foremost, an encapsulated format of the aluminothermic mixture that provides the advantages mentioned above. But it does not stop there, since such a format must necessarily dispense with the ignition powder, otherwise, and if such a format were to include both mixtures, one very close to the other to make ignition possible, there would be a great danger of such ignition being carried out accidentally, not necessarily during the execution of the weld, with the fatal consequences that can be imagined.
In short, the new k-cup or encapsulated format of the mixture is linked to a new reaction initiation system, which does not make use of ignition powder, and which is carried out remotely by means of an electronic device. This new reaction initiation system is a very differentiating element compared to other similar solutions on the market.
Are you ready for the evolution of the KLK weld?….
*PROYECTO CAPSULE
Research to obtain a new aluminothermic reaction initiation system with encapsulated format of the mixture.
Proyectos I+D Idepa, 2019 (Programa RIS3 Empresa)
IDE/2019/000320
The objective of the project is to develop an initiation system for the reaction of the aluminothermic mixture in exothermic welding. This system will simplify the installation process by eliminating ignition materials and reducing the preparation time by dispensing with the easily flammable second mixture of the initiation system currently employed, and will also allow the use of an encapsulated format of the aluminothermic mixture that confers reliability and safety.
PROJECT SUPPORTED BY:
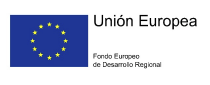
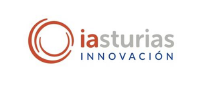

KLK Electro materiales slu
Mail | Web | Teléfono | Chatbot | Social Media
Need help?